Six Sigma Green Belt Training Certification
Efficiently using six sigma well to reduce defects and improve productivity
4.46 (13 reviews)
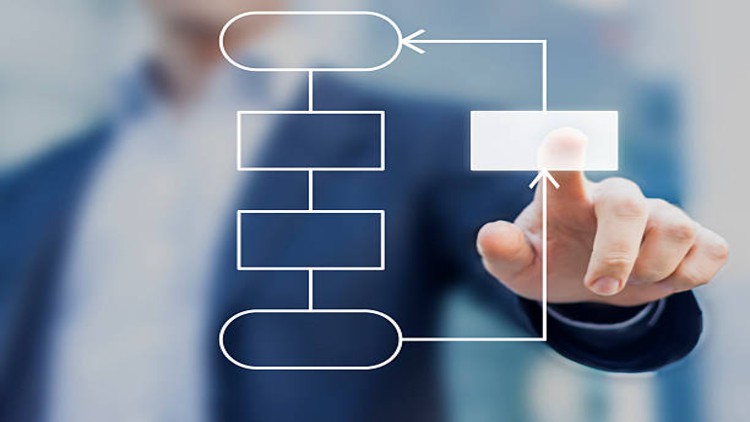
19
students
3.5 hours
content
Feb 2025
last update
$19.99
regular price
What you will learn
Six sigma history and application
Common six sigma principles
Continues process improvement: Toyota and Lean
Challenges of six sigma
Lean concept
Other process improvement and quality methods
Basic six sigma concept
Approaching the problem
Projects and processes
Critical to quality characteristics
Selecting the right projects
Basic six sigma team management
Introduction to DMAIC and DMADV
How to get six sigma certification
Screenshots
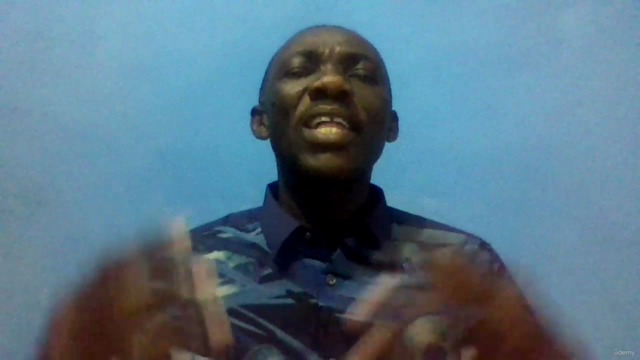
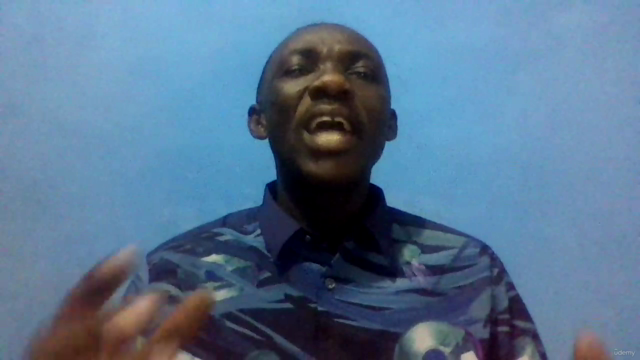
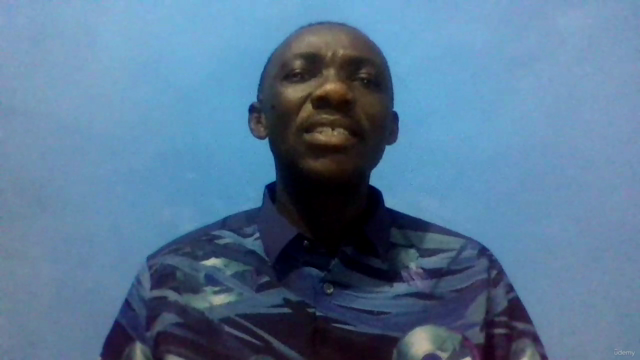
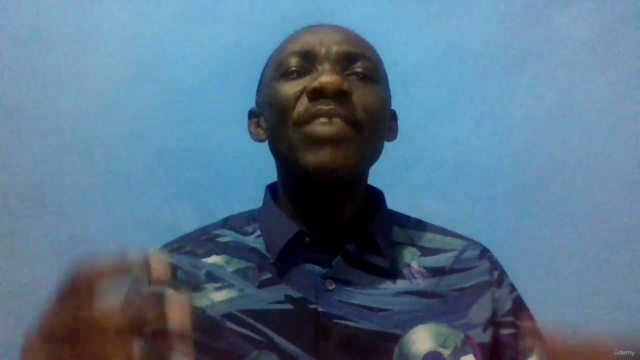
Related Topics
4226450
udemy ID
8/6/2021
course created date
8/17/2021
course indexed date
Bot
course submited by